greentec steel: Construction progress high and low
In 2027, our new electric arc furnace will go into operation. We are already securing its future supply. To ensure that raw materials and aggregates as well as green electricity are available for the EAF in time, we are working at full speed. With the completion of the conveyor belt bridge, which in the future – from a depth of 10 meters to a height of over 50 meters – will supply both the LD steelworks with aggregates and alloys as well as the electric arc furnace with HBI, an important project has still been completed.
The bridge to green steel
The supply highway at the voestalpine site in Linz stretches over 800 m from our new raw materials warehouse to the steel mill complex. The conveyor belt bridge will take over the supply of the LD steel mill from April 2024 and will also supply the new electric steel mill after its completion. The old conveyor system has to make way for the new construction of the electric steelworks, so the new conveyor belt bridge ensures the supply of alloys and aggregates to the existing LD3 steelworks. It is not a simple replacement, but has one more transport lane. On it, HBI, directly reduced iron ore, reaches the EAF.
Colossus on steel feet
Construction of the new conveyor belt bridge for the steelworks has been underway since August 2022. Its supports carry a total weight of 5,000 t for the construction alone. When fully operational, the transported goods are added: HBI, aggregates and alloying agents.
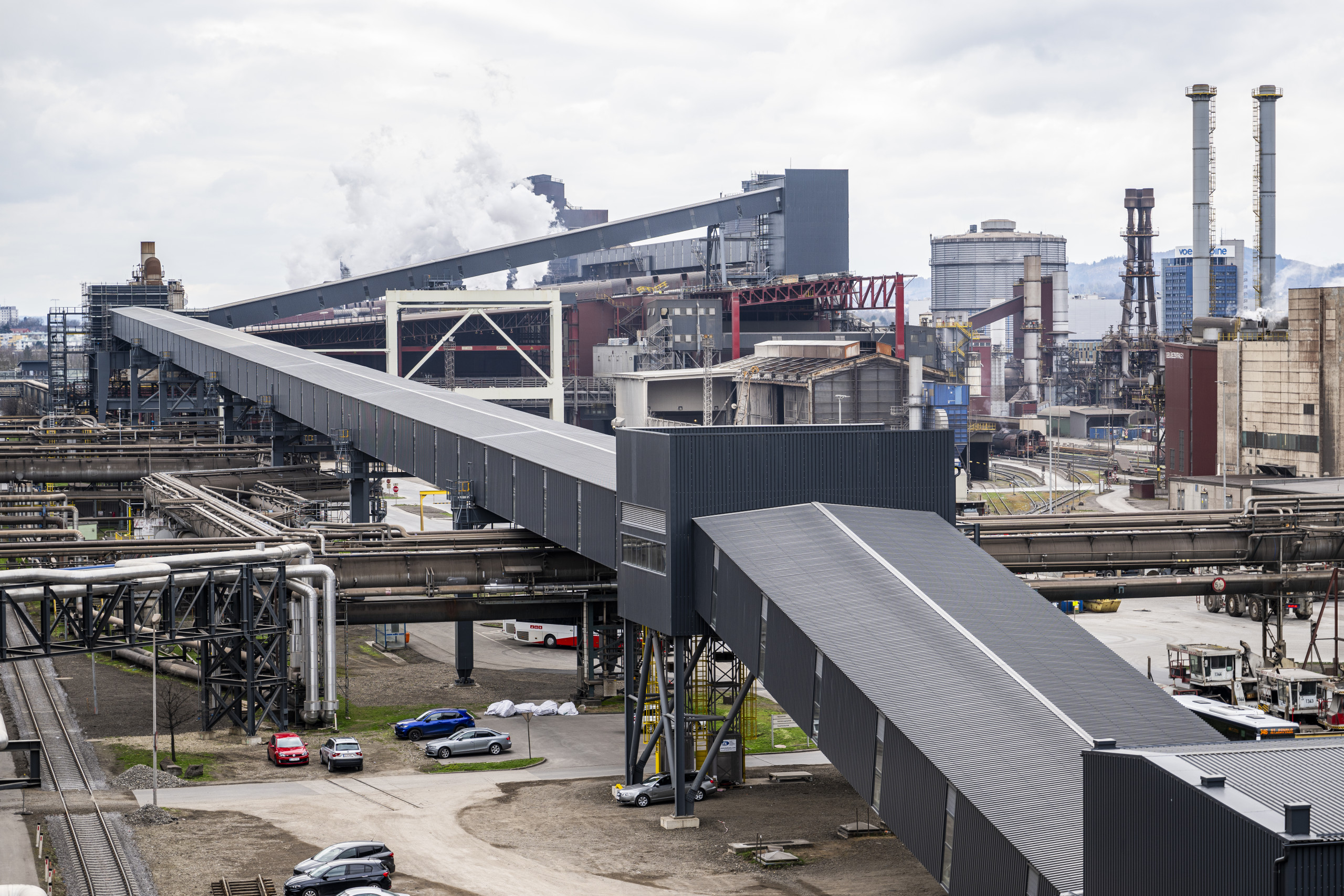
Even before its first use, the new conveyor belt bridge contributes to reducing emissions. Its cladding is made of voestalpine steel from the greentec steel edition: around 190 tons of steel with a reduced CO2 footprint are used to enclose the entire bridge. A real bridge to the world of green steel at voestalpine.
High voltage in the underground
It continues to be full of tension. The new EAF, which will go into operation from 2027, needs a lot of electricity. In order to be able to meet his needs, we are laying a 220 kV cable from the Hütte Süd junction in a microtunnel about 25 m below the factory facilities to the EAF site.
The 1,800 m long tunnel is flooded from the overlying water-bearing layers. The advantage: The water cools the extra-high-voltage cable with its 220 kilovolts and thus reduces the transport loss of electrical energy. Targeted pumping out of small quantities of water ensures efficient cooling, without which it would quickly become too warm in the tunnel.
The deep construction of this supply tunnel secures the path for our 220 kV line below all other underground supply and disposal channels. In any case, an exciting sub-project of our greentec steel program.
Well targeted underground
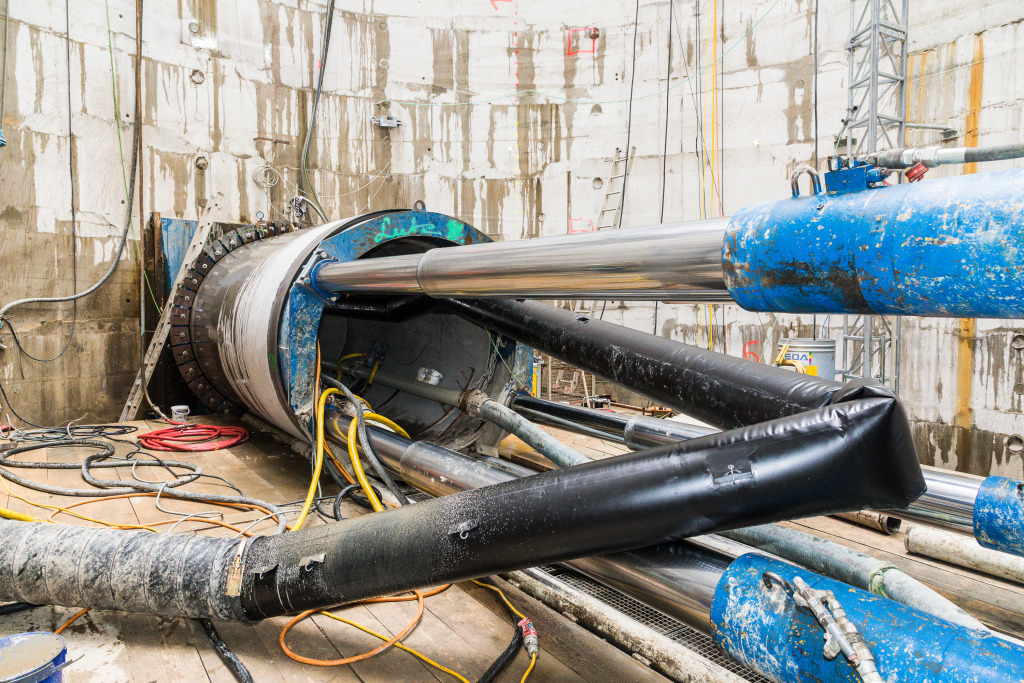
FAQs
-
Why an underground solution for the power supply line?
A high-voltage line would need space: for the pylons and the necessary distances to buildings and people. Therefore, we are placing the supply cable in a microtunnel.
-
How big will the microtunnel be?
The microtunnel will have an outer diameter of 2.60 m and an inner diameter of 2 m. It will reach a length of 1,800 m and run about 25 m below the plant facilities.
Why is the new conveyor belt bridge getting an additional lane?
In the future, what steel production requires will be delivered on three instead of the previous two. In addition to alloying agents and lime, hundreds of tons of HBI, directly reduced iron ore, are then fed into the EAF every day. Scrap and pig iron continue to come in special vehicles.
-